CLADDING- EN LASTECHNIEKEN
Cladding is a joining technique in which a material is pressed onto a carrier material under high pressure. The most famous form is laser cladding. Welding
is the joining of materials by means of heat and / or pressure, whereby
the filler material and the workpiece are mixed together.
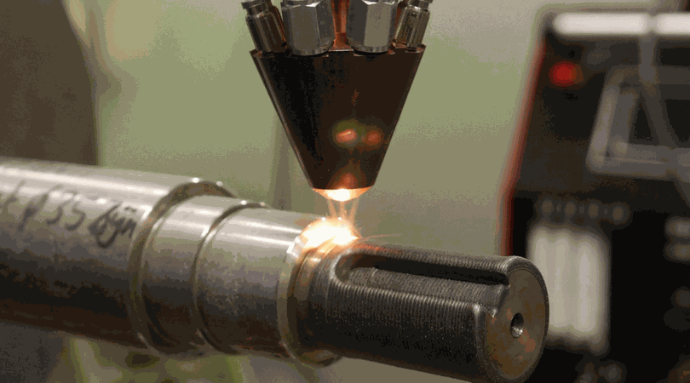
FUSIONLAYERS
When applying fusion layers, a thick and impact-resistant layer is applied to a part, making it very wear-resistant. The
melting layer (with melting point reducers) is first sprayed on and
then melted on the workpiece at a temperature of 1,100 ° C. As a result, the layer is attached to the part just like a welded layer. It is possible to use all kinds of combinations of materials when applying sealing layers.
Coatingmaterials
- Nickel/Cobalt
- Chrome alloys
Applications
- Pumpaxles
- Valve seats
- Gate Valves
- Transportscrews
- Thermowells
MMA, MIG/MAG & TIG-WELDING
Manual metal arc
welding (MMA), Metal Inert Gas / Metal Active Gas welding (MIG / MAG
welding) and Tungsten Inert Gas welding are forms of arc welding. MMA
welding is also known as stick welding. The charging processes are based
on an electric arc that fuses the surface of the workpiece and at the
same time fuses the material of an electrode or wire that you want to
apply. The processes are characterized by a relatively high mixing of
welded material and workpiece material (between 15 and 30%).
MMA
and TIG welding is mainly done manually. These processes are especially
suitable for smaller surfaces and applications along edges and
hard-to-access workpieces.
As a process, MIG welding is also
suitable for mechanization and automation and is therefore highly
controlled. This technique is more suitable for larger surfaces.
The
welded-on top layer is completely dense and metallurgically tightly
bonded to the workpiece, making it extremely impact and shock resistant.
Depending on the chosen welding material, the coating offers improved
wear resistance, corrosion resistance and / or high temperature
oxidation resistance.
Coatingmaterials
- Manganese steel, Cr steel and stainless steel
- Nickel-base (super)alloys
- Cobalt-base (super)alloys
- Carbides such as chrome- or tungstencarbide
Applications
- Wear resistant, impact and shock resistant
- Corrosion- en oxidation resistant
- Dimension recovery
PTA-WELDING
Plasma-transfered
arc welding (PTA welding) is a special variant of welding, which has
been specifically developed for the application of cover layers. A
concentrated plasma arc ensures, under the protection of argon and / or
helium, that the surface of a workpiece to be welded is fused. At the same time, welding powder fuses dosed with the base material. Characteristics
for this process are very low mixing of welded material and workpiece
material (3-7%), a small, heat-affected zone and precise process
control.
The welded-on coating is completely dense and metallurgically bonded to the workpiece. This makes the weld-on layer extremely impact and shock resistant. Depending
on the chosen welding material, the coating offers special wear
resistance, corrosion resistance and / or high temperature oxidation
resistance.
Coatingmaterials
- Cobalt-base (super)alloys
- Nickel-base (super)alloys
- Carbides such as chrome- or tungstencarbides
- Manganese steel, Cr steel and stainless steel
Applications
- Wear resistant, impact and shock resistant
- Corrosion- and oxidation resistance
- Dimension recovery
LASER CLADDING
Laser cladding is a welding technique that makes machine parts resistant to impact loads and for protection against corrosion. This process uses a focused laser beam to surface melt the workpiece and mix it with an added metal powder. With this you create a new (cover) layer on an existing workpiece of the machine part. The latest laser cladding processes are fast, have a very low heat input into the workpiece and exhibit minimal mixing of welded and workpiece material (<1%). Laser cladding can be controlled very accurately, so that we can weld very local and very specific material.
Coatingmaterials
- Cobalt-base (super)alloys
- Nickel-base (super)alloys
- Carbides such as chrome- or tungstencarbides
-
Cr-steel and stainless steel
Applications
- Wear resistant, impact and shock resistant
- Corrosion- and oxidation resistance
- Welding unusual materialcombinations
- Coatings on thin-walled workpieces
-
Complex and local dimensional restoration